The Ultimate Guide to CNC Lathe Parts for Metal Fabricators
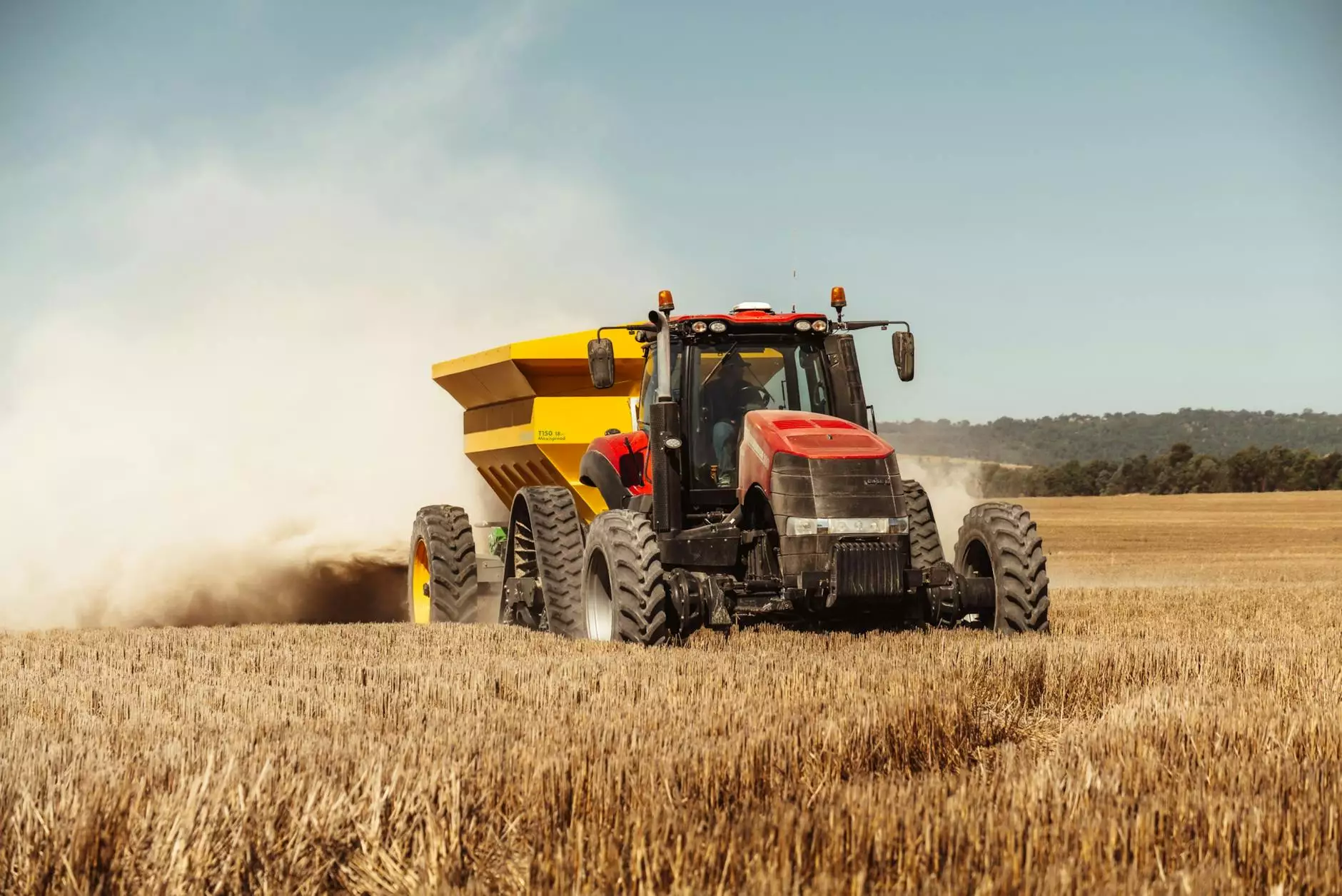
CNC lathe parts are essential components in the evolving world of metal fabrication. With the advent of advanced manufacturing techniques, understanding these parts can vastly improve efficiency, precision, and overall output quality for businesses like deepmould.net.
Understanding CNC Lathes
A CNC lathe, or computer numerical control lathe, is a machine tool that automates the turning process of cylindrical workpieces using programmable control. The significance lies in its ability to produce highly accurate components rapidly, making it invaluable for metal fabricators.
How CNC Lathes Work
CNC lathes operate by rotating a workpiece while a cutting tool shapes it, aligning precisely according to programmed specifications. This process significantly reduces human error and enhances production rates. Here are the core components involved:
- Spindle: The heart of the lathe that drives the workpiece.
- Tool Holder: Secures the cutting tools in place as they engage with the material.
- Bed: The base that supports and aligns all the machine's components.
- Control Unit: The interface through which operators input designs and specifications.
- Tailstock: Provides additional support for longer workpieces.
The Significance of CNC Lathe Parts in Metal Fabrication
In the competitive realm of metal fabrication, the quality and efficiency of production directly affect profitability. Here are several reasons why understanding cnc lathe parts is crucial for your business:
Precision and Accuracy
One of the primary benefits of CNC lathe parts is precision. Unlike manual machines, CNC lathes can repeatedly produce parts within extremely tight tolerances. This capability ensures that each part is identical to the last, which is especially important for large production runs.
Enhanced Productivity
Integrating CNC lathe parts into your manufacturing process can significantly enhance productivity. With automation, operators can run multiple machines simultaneously, increasing output without additional labor costs.
Cost-Effectiveness
Though the initial investment in CNC machines and their parts can be higher than traditional methods, the long-term savings in labor and waste reduction will outweigh the costs. This makes CNC machining a prudent choice for serious metal fabricators.
Key CNC Lathe Parts Every Fabricator Should Know
Understanding the different cnc lathe parts is essential for any fabricator looking to optimize their workflow. Here’s a breakdown of the most critical components:
1. Chuck
The chuck is the component that holds the workpiece in place. There are various types of chucks, including:
- Three-Jaw Chucks: Best for holding round pieces.
- Four-Jaw Chucks: Allow for better balance with irregular shapes.
- Collet Chucks: Offer precision for smaller parts.
2. Tool Post
The tool post is vital for holding and positioning the cutting tools. It allows for quick changes between different tools, improving efficiency when switching operations.
3. Servo Motors
Torque and control provided by servo motors ensure that CNC lathes operate smoothly and accurately, maintaining the quality and precision essential for metal fabrication.
4. Bearings
Bearings reduce friction in moving parts and are crucial in ensuring the longevity and reliability of CNC lathe components, impacting both performance and maintenance costs.
Maintenance Tips for CNC Lathe Parts
To ensure that your CNC lathe operates at peak efficiency, regular maintenance of cnc lathe parts is necessary. Here are some essential maintenance tips:
- Regular Cleaning: Dust and metal shavings can impede performance. Regular cleaning of the lathe, especially the bed and spindle, is essential.
- Lubrication: Proper lubrication of moving parts minimizes wear and ensures smooth operation.
- Inspect Tooling: Check cutting tools for wear and replace them as necessary to maintain precision.
- Calibration: Regularly calibrate your CNC lathe to ensure all components work together seamlessly, avoiding costly production errors.
The Future of CNC Lathe Parts and Metal Fabrication
The landscape of metal fabrication continues to evolve. With advancements in technology, including AI and machine learning, the future of CNC lathe parts looks promising. Here are key trends that will shape the future:
1. Smart CNC Machines
The integration of smart technology is revolutionizing the industry. These machines are capable of self-monitoring and predictive maintenance, reducing the likelihood of unexpected breakdowns.
2. Additive Manufacturing
As additive manufacturing technologies grow, the capabilities of CNC lathes are expanding. Combining subtractive and additive processes can lead to more complex geometries and improved design possibilities.
3. Sustainable Practices
As more companies strive for sustainable practices, the focus on reducing waste and improving energy efficiency will become a priority. Optimizing cnc lathe parts for sustainability will be key in the future.
Conclusion
In summary, understanding and investing in cnc lathe parts is critical for metal fabricators looking to stay competitive in today's market. By utilizing advanced CNC technologies and maintaining your equipment, you can enhance your manufacturing processes, improve product quality, and ultimately drive profitability. The insights shared in this article provide a foundation for businesses like deepmould.net to advance their operations in metal fabrication. Stay ahead of the competition by adopting the best practices and innovations in CNC technologies.