Innovative Applications and Advantages of the Volumetric Concrete Plant in Modern Construction
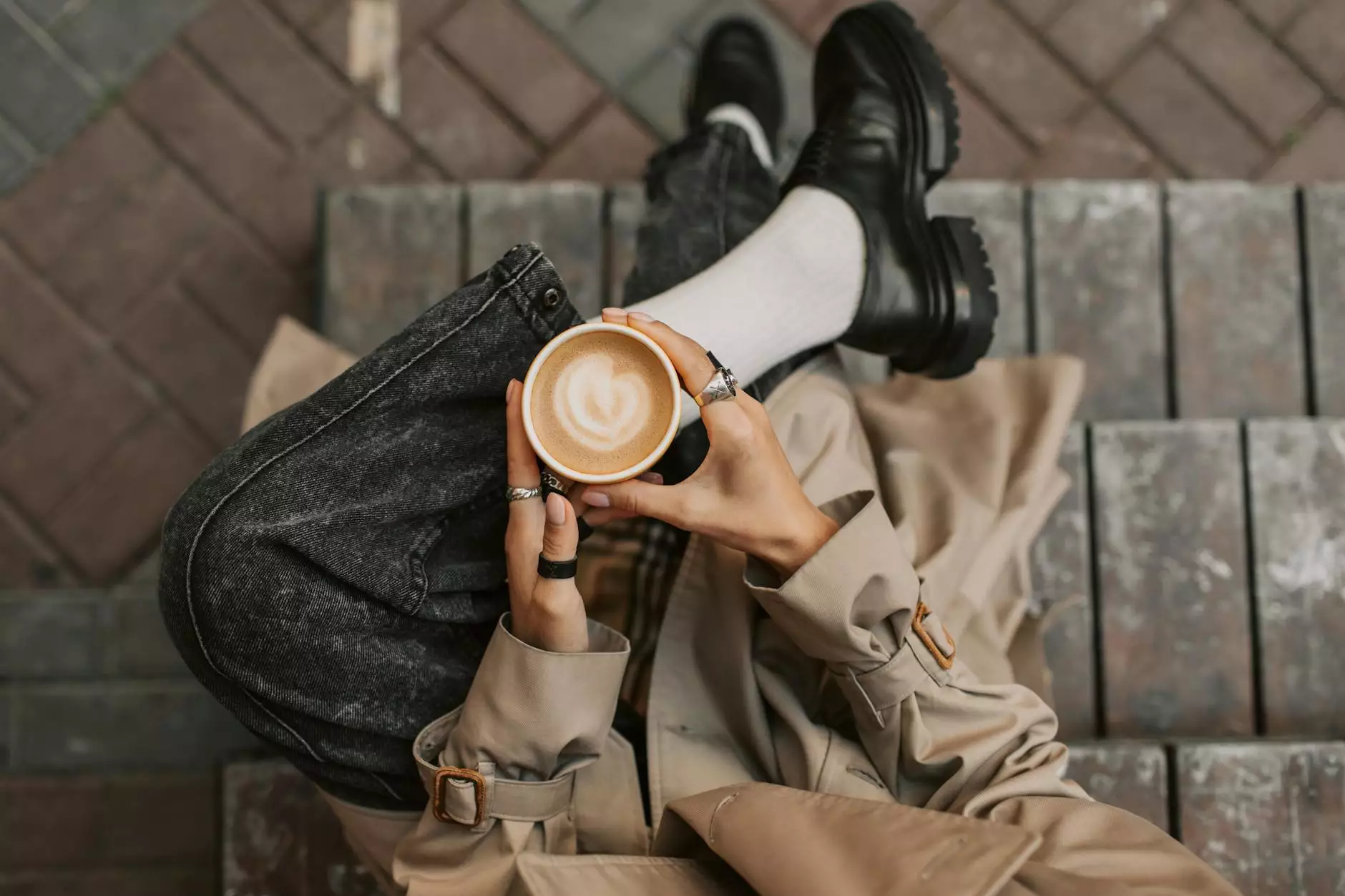
In today’s rapidly evolving construction industry, the demand for efficiency, precision, and sustainability has driven the adoption of advanced technological solutions. Among these innovations, the volumetric concrete plant stands out as a game-changer, revolutionizing the way concrete is produced, mixed, and delivered on-site. This comprehensive article explores the multifaceted benefits of volumetric concrete plant technology, its applications across various sectors, and why it is a vital component of modern construction projects.
Understanding the Volumetric Concrete Plant: Definition and Core Features
A volumetric concrete plant is a sophisticated, mobile, on-site batching system that combines raw ingredients—cement, aggregates, water, and additives—directly at the point of use. Unlike traditional central batching plants, these units are equipped with multiple compartments and computerized controls, enabling real-time, precise mixing tailored to specific project requirements.
Key features of a volumetric concrete plant include:
- Mobility: Compact and portable units capable of moving across multiple sites.
- On-Demand Mixing: Instantaneous batching and mixing based on demand, eliminating delays.
- Precision Control: Advanced digital controls ensure accurate proportions and quality consistency.
- Customization: Flexibility to produce different mix designs on-site, accommodating various structural needs.
- Reduced Waste: Minimizes overproduction and surplus, leading to significant cost savings and environmental benefits.
The Evolution of Concrete Production: From Traditional to Volumetric Technologies
Historically, concrete was produced in large central batching facilities and transported via mixer trucks to construction sites. This approach, while effective, posed challenges related to timing, freshness, waste, and logistical constraints.
The advent of the volumetric concrete plant aligns with the industry’s shift toward leaner, more flexible, and eco-friendly construction practices. By enabling on-site production, these systems eliminate many limitations of traditional methods, resulting in improved project management and quality output.
Key Advantages of the Volumetric Concrete Plant
1. Elevated Degree of Flexibility and Customization
One of the primary advantages is the ability to produce a wide array of concrete mixes tailored to specific structural requirements. This flexibility allows engineers and contractors to make real-time adjustments, optimizing mechanical properties such as slump, strength, and durability.
2. Superior Quality Control and Freshness
Since the concrete is mixed on-site, it is freshly prepared, reducing the risk of setting during transit. This leads to higher quality and consistency, which are critical for structural integrity and finish quality. Real-time monitoring ensures each batch adheres to required standards.
3. Cost Efficiency and Waste Reduction
On-site production significantly decreases transportation costs, especially for large projects or remote locations. Additionally, precise batching minimizes waste and excess materials, contributing to sustainable building practices and lowering overall project costs.
4. Reduced Dependency on External Suppliers
With a volumetric concrete plant, contractors gain greater control over supply timelines, avoiding delays caused by external supplier issues. This autonomy results in smoother project workflows and improved scheduling accuracy.
5. Enhanced Sustainability and Environmental Benefits
By producing only the necessary amount of concrete and reducing waste, these systems support eco-friendly construction methods. They also facilitate the use of recycled materials and supplementary cementitious agents, aligning with green building standards.
Technical Aspects and Operations of the Volumetric Concrete Plant
Advanced Control Systems and Automation
Modern volumetric concrete plants utilize state-of-the-art digital control panels, often integrated with tablet or smartphone interfaces. These systems allow operators to select mix designs, monitor quantities, and make adjustments in real-time, ensuring optimal performance and minimal human error.
Material Storage and Distribution Mechanisms
Multiple compartments are designed to store raw ingredients separately, with automated dispensing mechanisms regulated by the control system. This setup guarantees precise ingredient ratios and simplifies maintenance and refilling tasks.
Mixing Efficiency and Quality Assurance
The mixing process in a volumetric concrete plant is highly efficient, with twin horizontal or vertical mixing drums ensuring a homogeneous mix. In-line testing devices may also be integrated to verify properties before delivery.
Applications of the Volumetric Concrete Plant Across Industries
1. Commercial and Residential Construction
In urban and suburban settings, the volumetric concrete plant provides rapid, reliable concrete supply for foundations, slabs, columns, and finishing works. Its agility accelerates project timelines and enhances quality control.
2. Infrastructure Projects
Large-scale infrastructure, including bridges, tunnels, airports, and roads, benefits immensely from the consistency and on-demand production capabilities of these systems. The ability to produce high-strength or specialized concrete on-site is invaluable in such applications.
3. Remote and Mobile Constructions
For projects in isolated or difficult-to-access locations, portable volumetric concrete plants are essential. They reduce dependence on transportation and enable continuous supply in challenging environments.
4. Precast Concrete Manufacturing
Precast facilities utilize volumetric systems to ensure quality consistency and efficient batch production, which is crucial for high-volume manufacturing of panels, blocks, and other elements.
5. Emergency and Disaster Relief Construction
Rapid deployment systems allow emergency teams to quickly establish basic infrastructure, housing, and other facilities, demonstrating the adaptability and utility of on-site volumetric batching.
Choosing the Right Volumetric Concrete Plant: Factors to Consider
- Capacity: Match the plant's batching capacity with project size and expected throughput.
- Mobility: Consider the ease of transportation and setup in varying locations.
- Automation Level: Opt for systems with advanced control, monitoring, and connectivity features.
- Compatibility with Materials: Ensure the system can handle various ingredients, including recycled and specialty materials.
- Maintenance and Support: Choose reliable suppliers offering comprehensive after-sales support and training.
The Future of Volumetric Concrete Plants: Innovations and Trends
The landscape of concrete production is continuously evolving, with the volumetric concrete plant at the forefront of technological innovation. Emerging trends include:
- Integration with IoT: Enhancing real-time monitoring, predictive maintenance, and data analytics for optimal operation.
- Eco-friendly Materials: Incorporation of recycled aggregates and green cements to reduce environmental impact.
- Hybrid Systems: Combining volumetric plants with traditional batching for maximum flexibility.
- Automation and Robotics: Fully automated systems capable of adjusting mixes without human intervention.
Conclusion: Embracing the Volumetric Concrete Plant Revolution
In summary, the volumetric concrete plant represents a pivotal advancement in the construction industry, offering unparalleled flexibility, quality, and sustainability. Its capability to produce fresh, customized concrete on-demand makes it an indispensable tool for diverse projects, from urban infrastructure to remote construction sites.
As technology progresses and environmental considerations become increasingly important, the role of these systems will only expand. Embracing volumetric concrete plant technology today positions construction firms at the forefront of innovation, efficiency, and green building practices.
For more insights and high-end solutions, visit polygonmach.com, where industry-leading electronic and 3D printing technologies converge to redefine the possibilities of modern construction.