Understanding Die Cast Mold Manufacturers: The Backbone of Quality Production
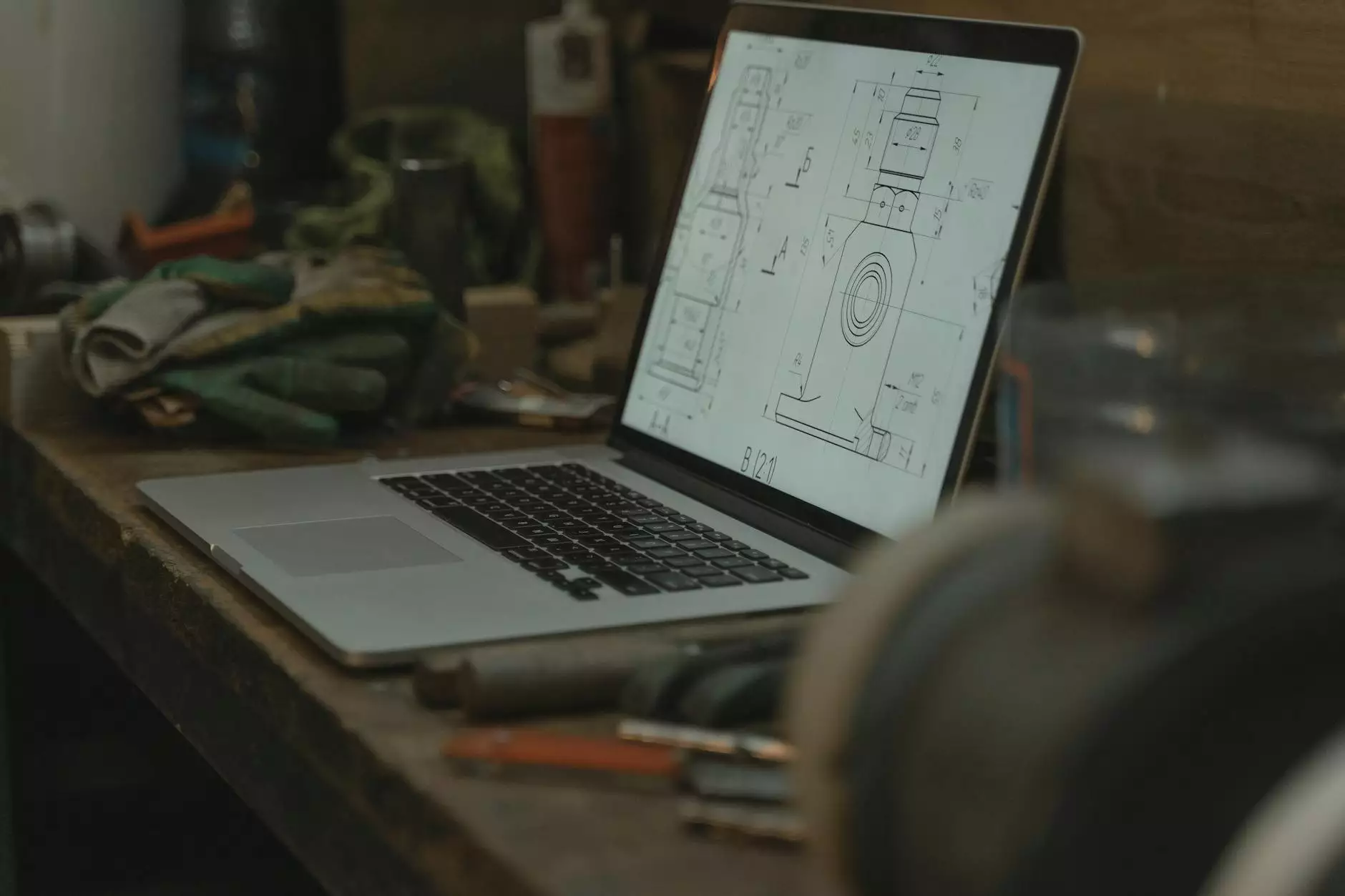
In the competitive landscape of modern manufacturing, die cast mold manufacturers play a pivotal role. These specialized suppliers provide critical assets that drive efficiency, precision, and quality in the production of various metal components. Understanding their importance is essential for anyone involved in the manufacturing process. This article dives deep into the functions, advantages, and the overall ecosystem surrounding die cast mold manufacturing.
What is Die Casting?
Before exploring the manufacturers, it’s crucial to grasp the concept of die casting itself. Die casting is a metal casting process that involves forcing molten metal under high pressure into a mold cavity. This process yields parts with exceptional dimensional accuracy and a superior surface finish. Here are some key points about die casting:
- Materials used: Common materials include aluminum, zinc, and magnesium due to their lightweight and durable properties.
- High production rates: Die casting is known for its ability to produce large quantities of parts quickly.
- Complex shapes: The process can achieve intricate designs that would be difficult or impossible with other manufacturing methods.
Role of Die Cast Mold Manufacturers
Die cast mold manufacturers are crucial players in the die casting process. Their primary function is to design and fabricate the molds that define the shape of the finished products. Without these manufacturers, the quality and efficiency of die casting would be significantly compromised. Here’s how they contribute:
Mold Design and Engineering
The journey begins with design. Manufacturers must create molds that not only capture the desired shape but also withstand the high pressures and temperatures involved in the die casting process. This involves:
- 3D modeling: Using sophisticated software to create precise digital models of the molds.
- Finite Element Analysis (FEA): Analyzing the mold to anticipate how it will react under various conditions.
- Cooling systems: Designing effective cooling channels within the mold to ensure consistent cooling and reduce cycle time.
Mold Fabrication Techniques
Once the design is approved, the fabrication process begins. Various techniques are utilized by mold manufacturers to bring designs to life, including:
- Machining: High-precision CNC machines cut and shape the mold components from solid blocks of material.
- Electro-discharge machining (EDM): A process that allows for intricate design features that are challenging to achieve through traditional machining.
- 3D printing: Emerging as a viable option where rapid prototyping of mold components is needed.
Benefits of Engaging with Die Cast Mold Manufacturers
Partnering with experienced die cast mold manufacturers brings numerous advantages to businesses. Here, we explore some of these critical benefits:
Quality Assurance
Professional manufacturers enforce stringent quality control processes at every stage, from design to production. This ensures that the molds produce parts with flawless accuracy, helping brands maintain high-quality standards.
Cost Efficiency
Investing in high-quality molds leads to longer lifespans and reduced maintenance costs. By working with skilled manufacturers, businesses can streamline production processes, minimizing waste and downtime.
Innovation and Customization
Every industry is different, and a one-size-fits-all approach does not apply. Experienced die cast mold manufacturers understand the nuances of individual business needs and can create customized solutions that enhance productivity and efficiency.
Choosing the Right Die Cast Mold Manufacturer
With numerous suppliers available, selecting the right die cast mold manufacturers can be daunting. However, there are key factors to consider that can ease your decision-making process:
Experience and Reputation
Researching the manufacturer's history and reputation within the industry is vital. Look for companies that have established a strong track record of success, including testimonials and case studies from past clients.
Technology and Capability
In today’s fast-paced environment, utilizing advanced technologies is essential. Evaluate whether the manufacturer employs modern techniques and machinery that align with your project requirements.
Support and Communication
Effective communication is key to a successful partnership. Ensure that the manufacturer is responsive to inquiries and willing to provide comprehensive support throughout the molding process.
Common Industries Utilizing Die Cast Molds
Die cast molds are not restricted to a single industry; their applications are widespread. Several sectors benefit significantly from this manufacturing technique:
- Automotive: Parts such as engine components and housings are often produced using die casting for their lightweight and durable properties.
- Aerospace: Strict tolerances and high-performance needs in aerospace components make die casting a go-to choice for manufacturers.
- Consumer Electronics: Enclosures and housing components in electronics are increasingly manufactured using die casting to ensure aesthetic appeal along with functionality.
- Industrial Machinery: Components that require extreme durability and precision often rely on die casting processes.
The Future of Die Cast Mold Manufacturing
The field of die cast mold manufacturing is poised for exciting developments in the coming years.
Technological Advances
The rise of Industry 4.0 will reshape manufacturing landscapes, with advancements in automation, artificial intelligence, and IoT. These innovations promise to enhance mold design, manufacturing efficiency, and production quality.
Sustainability Efforts
As global awareness of environmental concerns grows, manufacturers are increasingly adopting sustainable practices. This includes utilizing recycled materials, reducing waste in the production process, and improving energy efficiency.
Global Trends
The demand for die casting continues to rise as industries recognize the benefits of this manufacturing process. Manufacturers must remain agile and responsive to global market trends, including shifts in consumer demand and the availability of raw materials.
Conclusion
In summary, die cast mold manufacturers are vital to the success of diverse manufacturing endeavors. They not only provide the means for crafting high-quality products but also contribute significantly to efficiency and innovation. As industries evolve, the partnership between manufacturers and die casting providers will only strengthen, underpinning the need for precision and excellence in production.
For businesses looking to explore the potential of die casting, or if you are seeking a reliable partner in this field, consider reaching out to top-notch die cast mold manufacturers. With the right collaboration, you can enhance your product quality and make strides in your competitive landscape.
For more information about exceptional metal fabrication and die cast solutions, visit Deep Mould.