Understanding Tube Fittings Dimensions for Optimal Selection
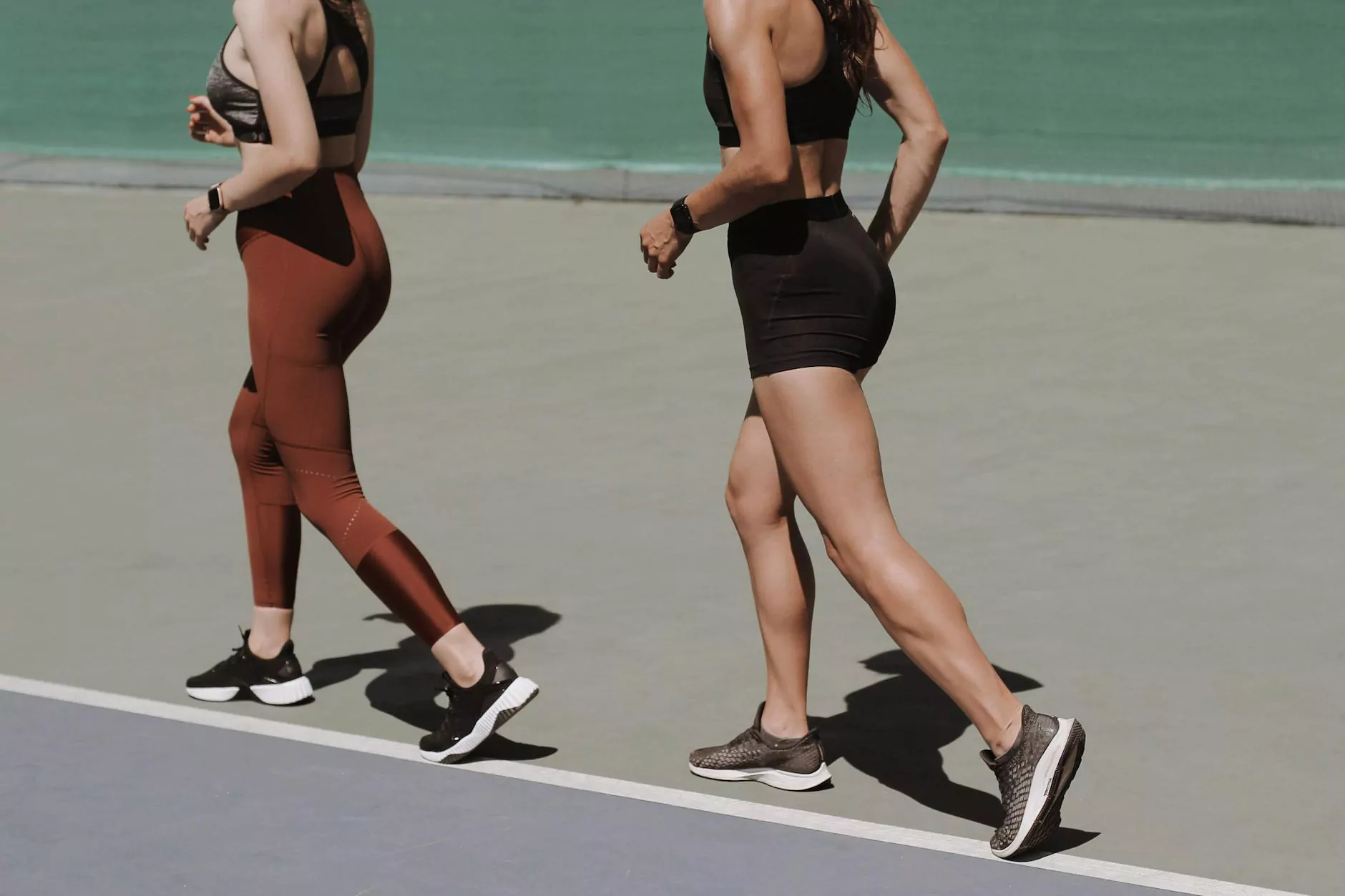
When it comes to fluid and gas systems, the importance of selecting the right tube fittings cannot be understated. These critical components ensure that your piping system functions efficiently and effectively. Understanding the tube fittings dimensions is pivotal in making the correct choice for your specific application. In this article, we will delve deep into the various aspects of tube fittings dimensions, types, and the factors to consider when choosing the right fittings for your needs.
What Are Tube Fittings?
Tube fittings are mechanical devices that connect pipes, tubes, and hoses in various industrial applications. They help facilitate the flow of fluids or gases through pipelines while providing leak-free performance. The correct fitting ensures system integrity and plays a significant role in the overall efficiency of fluid transport systems.
Types of Tube Fittings
There is a myriad of tube fittings available in the market, each designed for specific applications. Here’s a comprehensive list of the common types of tube fittings you might encounter:
- Ferrule Fittings
- Forged Pipe Fittings
- Threaded Pipe Fittings
- Flanges
- Check Valves
- Ball Valves
- Needle Valves
- Manifold Valves
- Double Ferrule Tube Fittings
- Single Ferrule Tube Fittings
- NPT Fittings
- General Tube Fittings
The Importance of Tube Fittings Dimensions
Understanding tube fittings dimensions is crucial for several reasons:
- Ensuring Compatibility: The dimensions dictate how well a fitting will connect with pipes or tubes, impacting the overall system integrity.
- Maintaining Flow Efficiency: Properly sized fittings minimize pressure drops and maximize flow rates.
- Preventing Leaks: Correct dimensions ensure a tight seal, reducing the chances of leakage that can lead to performance issues and hazards.
Key Tube Fitting Dimensions to Consider
When evaluating tube fittings, several dimensions are critical to ensure compatibility and performance:
1. Outer Diameter (OD)
The outer diameter (OD) of a tube fitting is fundamental when ensuring a proper fit within the piping system. It is the total width across the outer rim of the fitting and typically needs to match the OD of the attached tubing.
2. Inner Diameter (ID)
The inner diameter (ID) is equally important as it influences the flow characteristics of the fluid or gas being transported. A larger ID facilitates a higher flow rate.
3. Wall Thickness
The wall thickness of the tube fitting will affect its pressure rating, durability, and ability to withstand external pressures and temperatures. It’s crucial to choose a fitting with an appropriate wall thickness for your application.
4. Thread Size and Type
For threaded fittings, the thread size and type (NPT, BSPT, etc.) determine how securely two components can be connected. Understanding thread specifications is essential for leak-free installations.
Selecting the Right Tube Fitting for Your Application
Choosing the correct tube fitting involves understanding not only the dimensions but also the specific needs of your application:
1. Determine the Fluid Being Transported
The type of fluid or gas you are working with can significantly influence your choice. Some materials can corrode or degrade certain types of fittings, so it is critical to choose compatible materials.
2. Assess the Operating Conditions
Consider the pressure and temperature conditions your fittings will experience. Each fitting has ratings that define its operational limits, making it essential to select fittings that can handle your specific conditions.
3. Evaluate the Environment
Tube fittings must endure their surrounding environment. Factors like exposure to chemicals, moisture, and extreme temperatures will dictate the materials and designs that are suitable. For instance, stainless steel fittings may be more suitable for corrosive environments.
Common Materials Used in Tube Fittings
Different materials offer unique advantages for tube fittings:
- Stainless Steel: Highly resistant to corrosion and high temperatures, ideal for harsh environments.
- Brass: Offers excellent corrosion resistance and is commonly used in plumbing applications.
- Plastic: Lightweight and resistant to corrosion, suitable for low-pressure applications.
- Aluminum: Lightweight and strong, often used in automotive applications.
Installation Best Practices for Tube Fittings
To ensure the longevity and performance of your fittings, follow these installation best practices:
1. Prepare the Surface
Ensure that the surfaces of the pipes and fittings are clean and free from debris. Any foreign particles can lead to leaks or weak connections.
2. Use Proper Tools
Using tools designed specifically for tube fittings is essential. Improper tools can strip threads or damage fittings.
3. Check Alignment
Ensure that your fittings are aligned properly before tightening. Misalignment can create excessive stress on fittings, leading to premature failure.
Conclusion
In conclusion, the significance of tube fittings dimensions cannot be overstated. Selecting the right tubing and fittings ensures optimal performance, prevents leaks, and enhances the longevity of your piping system. By understanding the various tube fitting types, critical dimensions, and factors influencing your choices, you can make informed decisions that contribute to the success of your projects.
For high-quality tube fittings, ferrule fittings, forged pipe fittings, and more, visit techtubes.in. Our extensive range of products and expert guidance will help you find precisely what you need for your application.